In this article, we will explore how SLS 3D printing technology is reshaping manufacturing processes, enabling innovation, and driving efficiency. From aerospace to healthcare, automotive to consumer goods, SLS 3D printing is revolutionizing the way products are designed, prototyped, and manufactured. Join us as we delve into the world of SLS 3D printing and discover its incredible potential.
The Rise of SLS 3D Printing
SLS 3D printing, also known as Selective Laser Sintering, is a cutting-edge additive manufacturing technique that utilizes a high-powered laser to fuse powdered materials together, layer by layer, to create three-dimensional objects. This technology has gained significant momentum in recent years due to its versatility, precision, and ability to produce complex geometries that were previously unattainable through traditional manufacturing methods.

Advantages of SLS 3D Printing
2.1 Unparalleled Design Freedom
One of the key advantages of SLS 3D printing is its ability to achieve unparalleled design freedom. Unlike traditional manufacturing processes, which often impose limitations on the complexity of shapes and structures, SLS 3D printing allows for the creation of intricate designs with intricate details. This opens up a world of possibilities for designers and engineers, enabling them to push the boundaries of innovation.
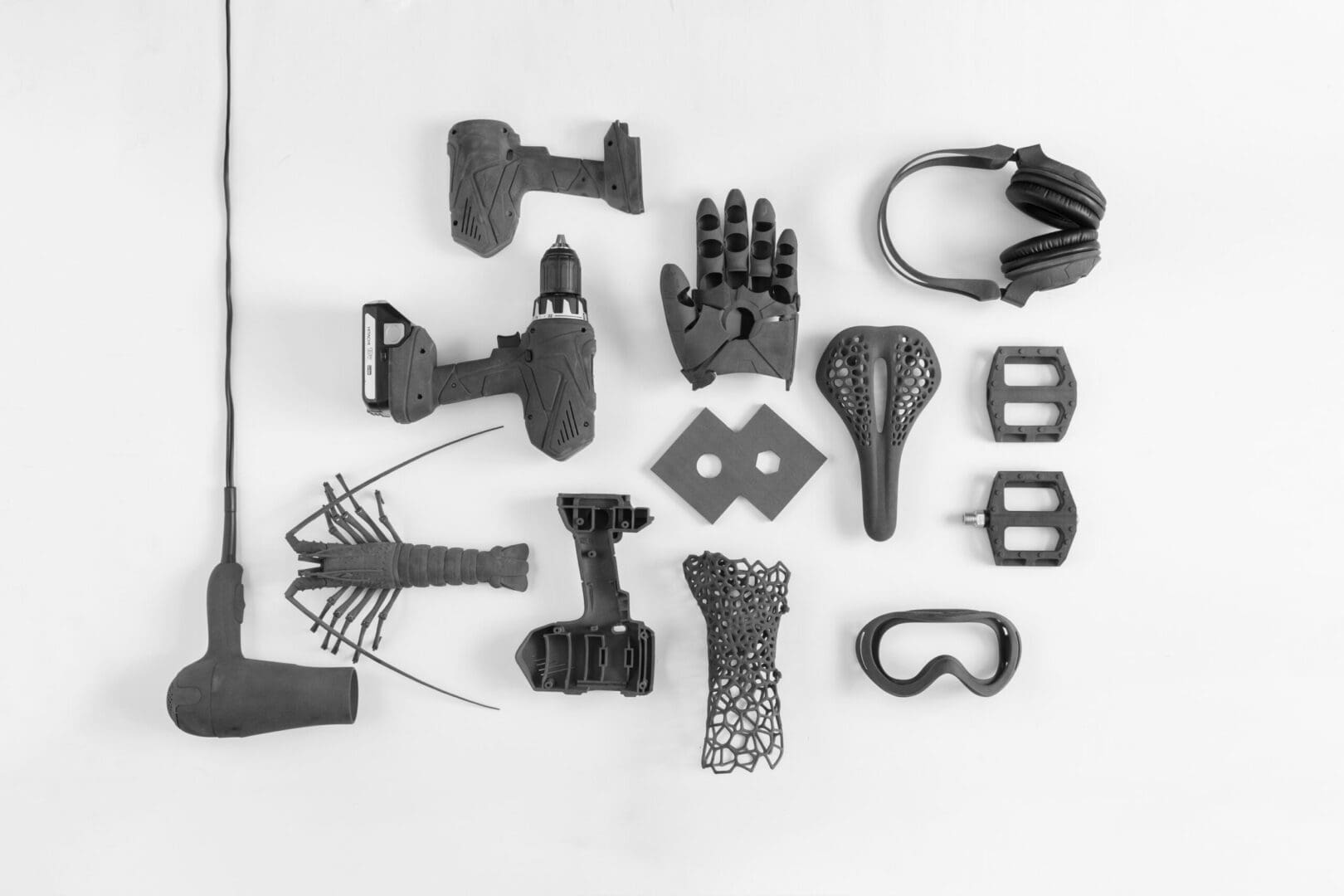
2.2 Cost-Efficiency and Time Savings
SLS 3D printing offers significant cost and time savings compared to traditional manufacturing methods. With SLS, there is no need for expensive molds or tooling, reducing upfront costs. Additionally, the ability to consolidate multiple parts into a single print job eliminates the need for assembly, streamlining the production process and reducing labor costs. Moreover, SLS 3D printing enables rapid prototyping, allowing for quick iterations and faster time-to-market.
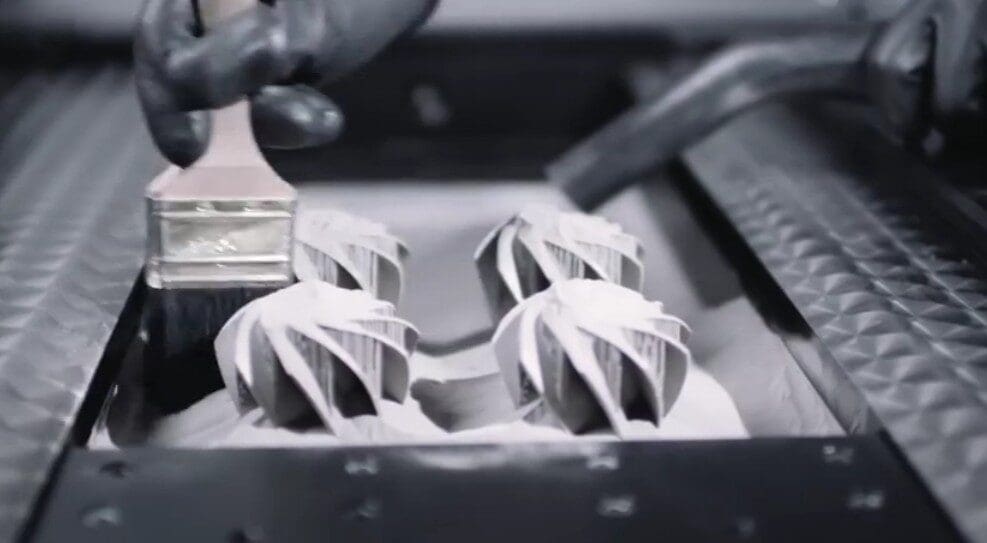
2.3 Material Versatility
Selective Laser Sintering supports a wide range of materials, including polymers, metals, and composites. This versatility makes SLS 3D printing suitable for various industries, each with its unique material requirements. From high-strength aerospace components to biocompatible medical implants, SLS 3D printing can accommodate diverse applications, providing tailored solutions for different industries.
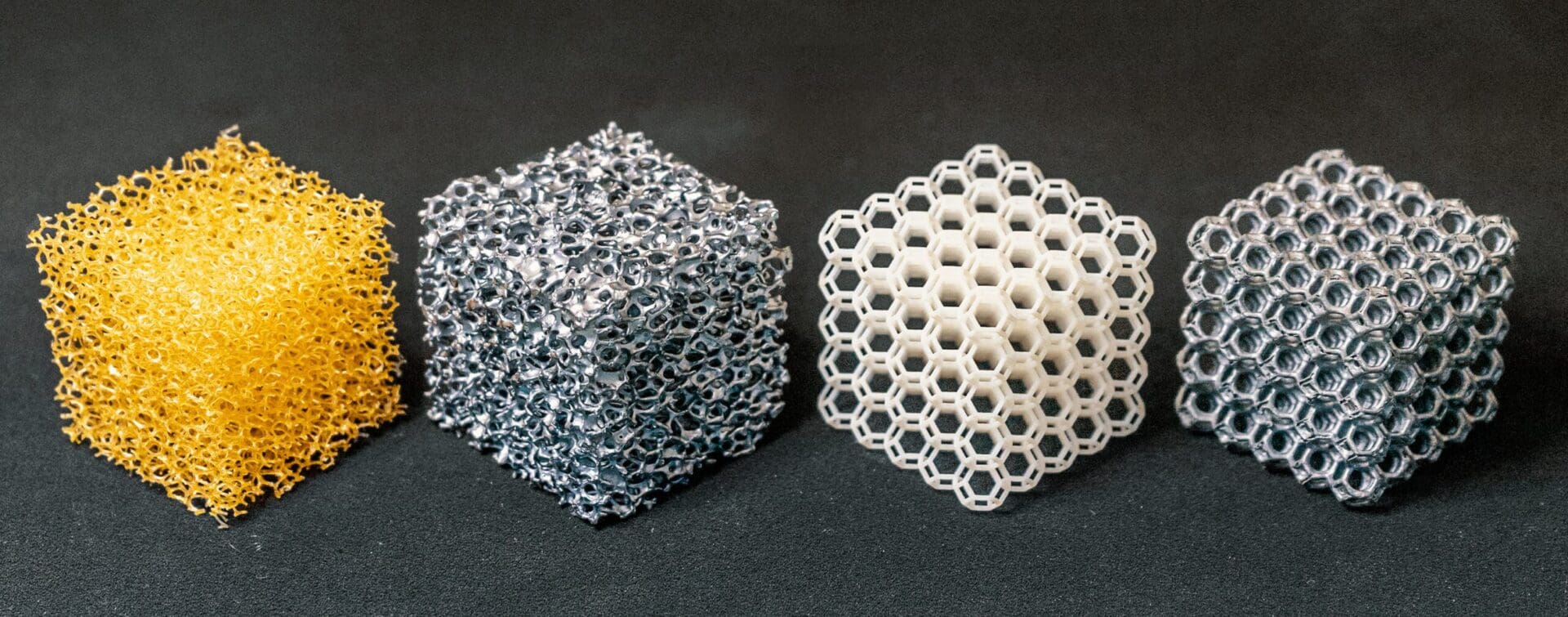
SLS 3D Printing in Aerospace
3.1 Lightweighting and Complex Geometries
The aerospace industry has embraced SLS 3D printing for its ability to create lightweight components without compromising strength. By utilizing lattice structures and optimizing designs for weight reduction, SLS 3D printing enables the production of complex geometries that enhance fuel efficiency and reduce aircraft weight, leading to significant cost savings and environmental benefits.
3.2 Rapid Prototyping and Customization
SLS 3D printing allows aerospace engineers to rapidly prototype and iterate designs, reducing development time and costs. Moreover, it enables the customization of parts for specific aircraft models, ensuring a perfect fit and improved performance. Whether it’s creating intricate air ducts or lightweight brackets, SLS 3D printing empowers the aerospace industry to innovate and stay ahead of the competition.
3.3 On-Demand Spare Parts
Maintenance and repair operations in the aerospace industry often face challenges in sourcing obsolete or hard-to-find spare parts. SLS 3D printing offers a solution by enabling the on-demand production of spare parts, eliminating the need for costly inventory management and reducing downtime. This capability ensures a more efficient supply chain and enhances the overall operational readiness of aircraft.
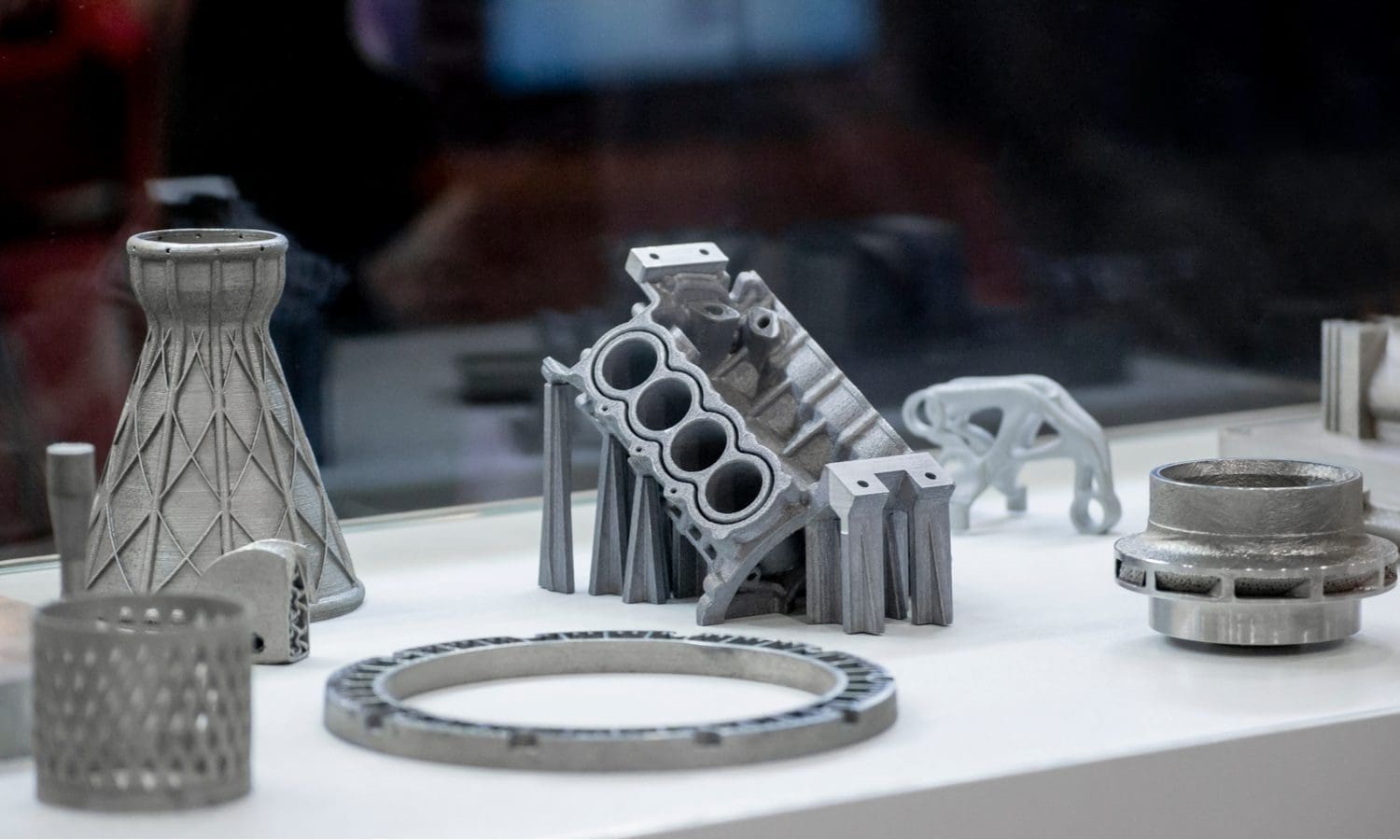
SLS 3D Printing in Healthcare
4.1 Patient-Specific Medical Devices
SLS 3D printing has revolutionized the healthcare industry by enabling the production of patient-specific medical devices. From prosthetics to orthotics, SLS 3D printing allows for the customization of devices to match the unique anatomical needs of each patient. This personalization improves patient comfort, functionality, and overall treatment outcomes.
4.2 Surgical Guides and Implants
In complex surgical procedures, precision and accuracy are paramount. SLS 3D printing facilitates the production of surgical guides and implants with exceptional accuracy, ensuring optimal surgical outcomes. Surgeons can use patient-specific guides to navigate complex anatomical structures, reducing surgical time and improving patient safety. Additionally, SLS 3D printing enables the creation of biocompatible implants that perfectly match the patient’s anatomy, enhancing post-operative recovery.
4.3 Pharmaceutical Applications
SLS 3D printing is also making strides in the pharmaceutical industry. It enables the production of personalized drug delivery systems, such as customized tablets with specific dosages and release profiles. This technology has the potential to revolutionize the field of personalized medicine, allowing for tailored treatments based on individual patient needs.
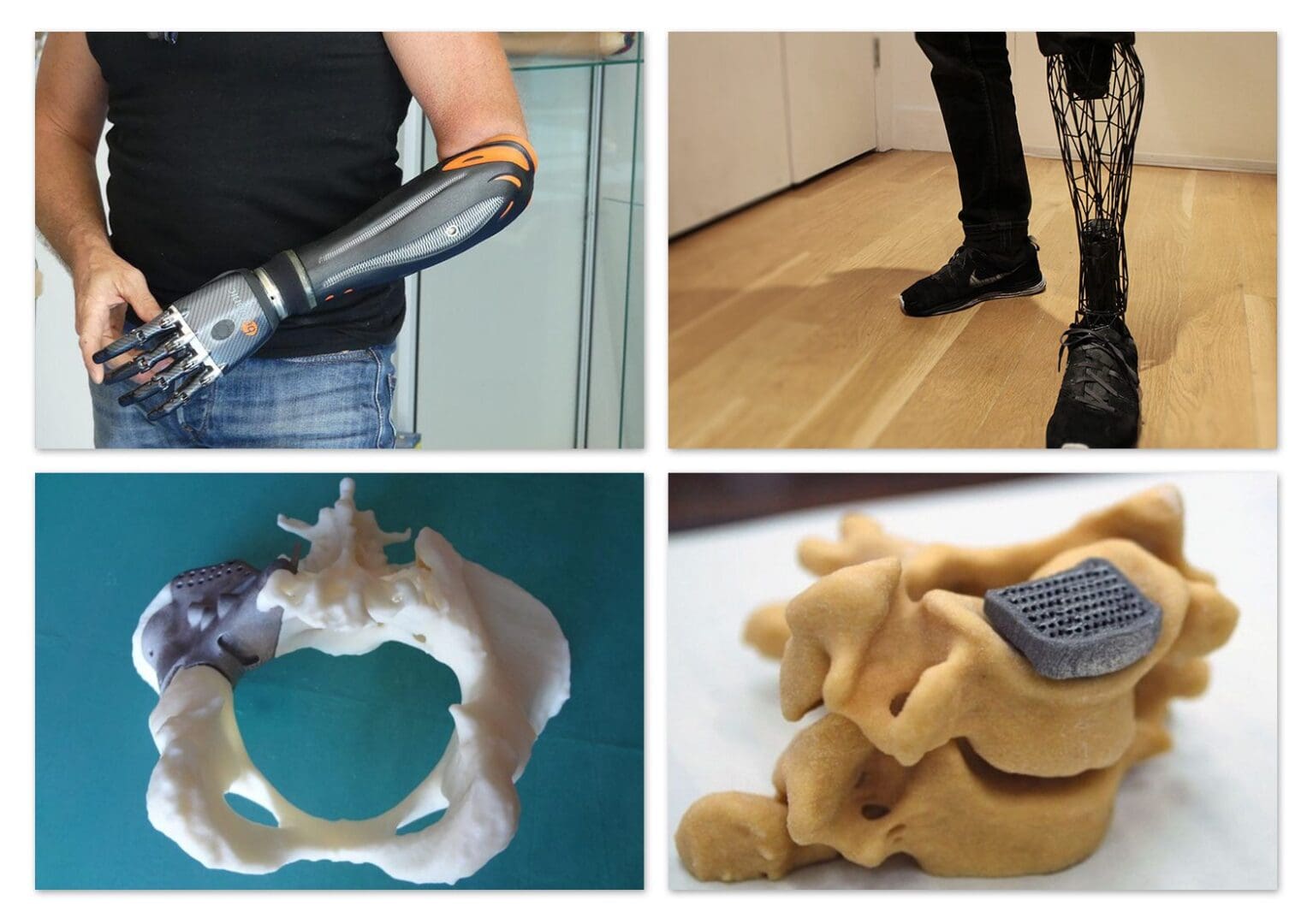
SLS 3D Printing in Automotive
5.1 Lightweighting and Performance Optimization
The automotive industry is leveraging SLS 3D printing to achieve lightweighting and optimize vehicle performance. By replacing traditional metal components with lightweight, high-strength polymer parts, SLS 3D printing helps reduce vehicle weight, leading to improved fuel efficiency and reduced emissions. Moreover, SLS 3D printing enables the creation of complex internal structures that enhance structural integrity and crashworthiness.
5.2 Customization and Interior Design
SLS 3D printing allows automotive manufacturers to offer customized interior components, such as dashboard panels, center consoles, and door handles. With SLS, designers can create intricate textures, patterns, and personalized branding, providing a unique and luxurious experience for customers. This customization potential sets automotive brands apart and enhances customer satisfaction.
5.3 Tooling and Jigs
SLS 3D printing is also transforming the production of tooling and jigs in the automotive industry. These manufacturing aids can be quickly produced using SLS technology, reducing lead times and costs associated with traditional machining methods. By leveraging SLS 3D printing for tooling, automotive manufacturers can achieve faster production cycles and improve overall operational efficiency.
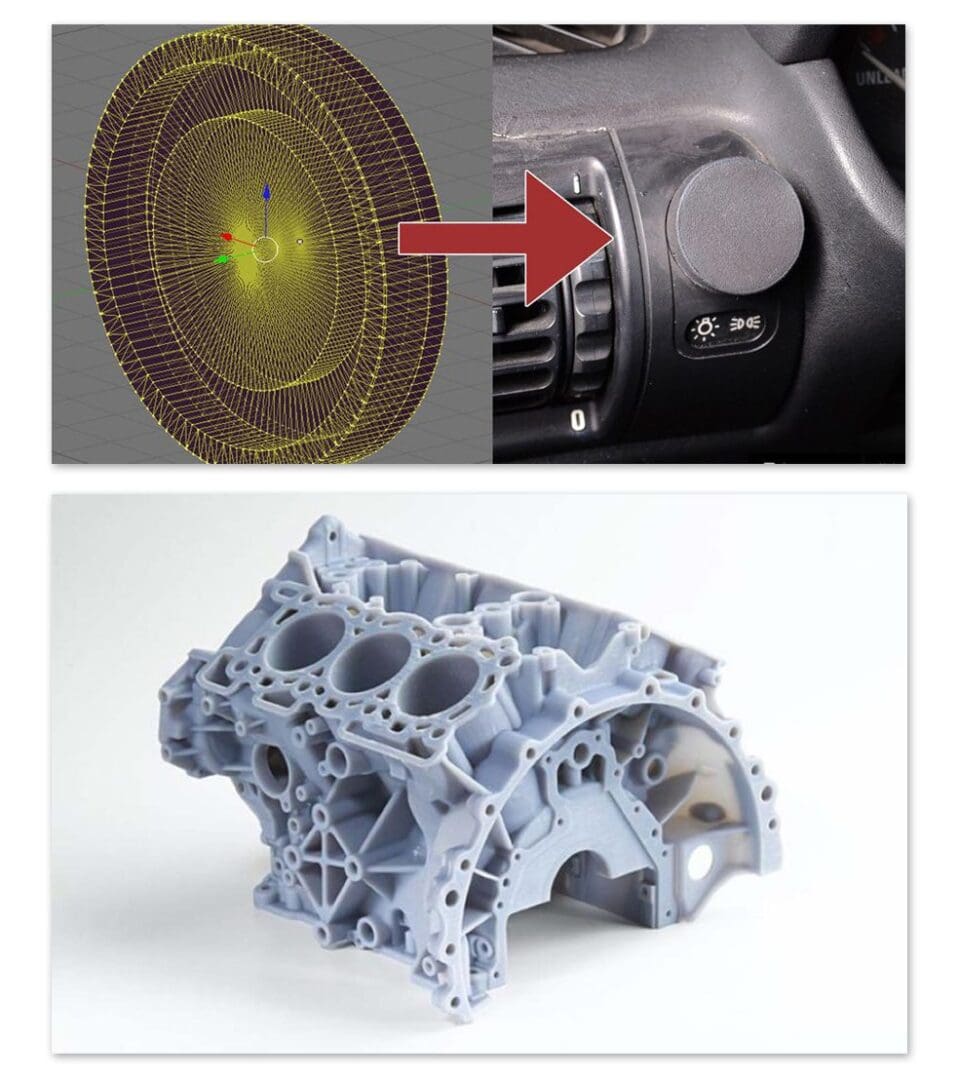
SLS 3D Printing in Consumer Goods
6.1 Customized Wearables and Accessories
SLS 3D printing is revolutionizing the consumer goods industry by enabling the production of customized wearables and accessories. From personalized jewelry to bespoke eyewear, SLS technology allows consumers to express their individuality through unique, one-of-a-kind products. This customization potential opens up new business opportunities and enhances brand loyalty.
6.2 Rapid Prototyping and Iteration
In the fast-paced world of consumer goods, speed to market is crucial. SLS 3D printing enables rapid prototyping and iteration, allowing designers and manufacturers to quickly test and refine their product concepts. This agility helps companies stay ahead of trends, respond to consumer demands, and reduce time-to-market, giving them a competitive edge in the industry.
6.3 Supply Chain Optimization
By adopting SLS 3D printing, consumer goods companies can optimize their supply chains and reduce inventory costs. With on-demand production capabilities, manufacturers can produce goods as needed, eliminating the need for large warehouses and excess inventory. This lean approach streamlines operations, minimizes waste, and improves overall supply chain efficiency.
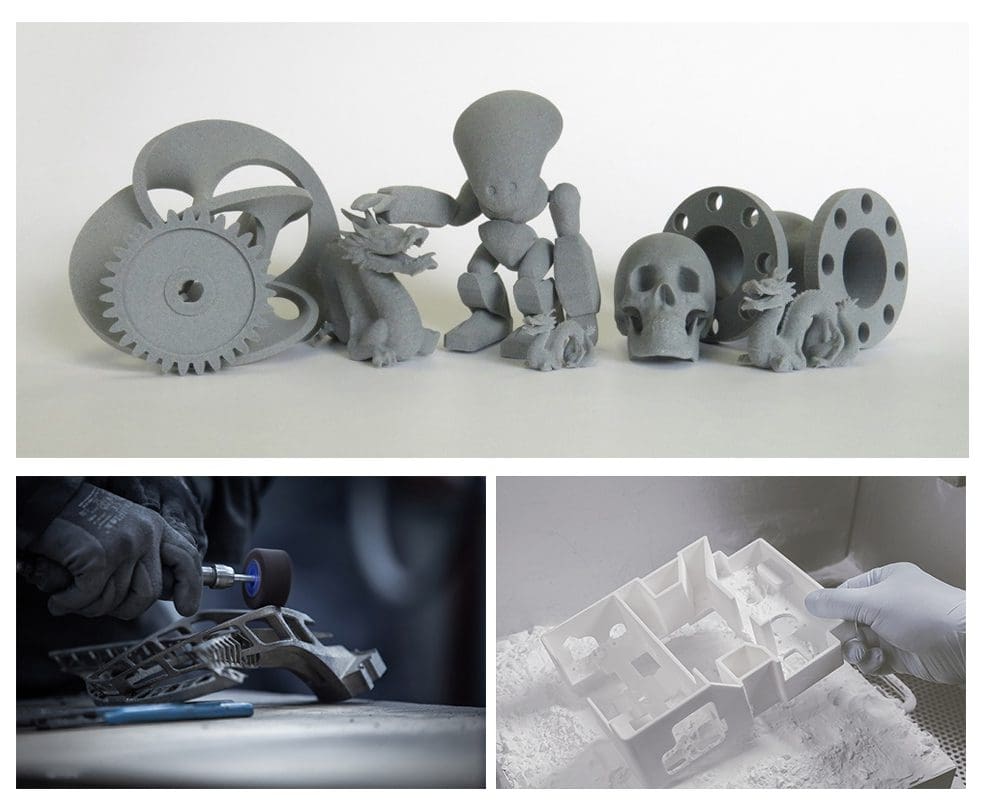
Selective Laser Sintering (SLS) 3D printing is transforming industries across the board, from aerospace and healthcare to automotive and consumer goods. Its unparalleled design freedom, cost-efficiency, and material versatility make it a game-changer in the world of additive manufacturing. As SLS technology continues to evolve and mature, we can expect even more groundbreaking applications and innovations in the future. Embrace the power of SLS 3D printing and unlock the potential of additive manufacturing for your industry.